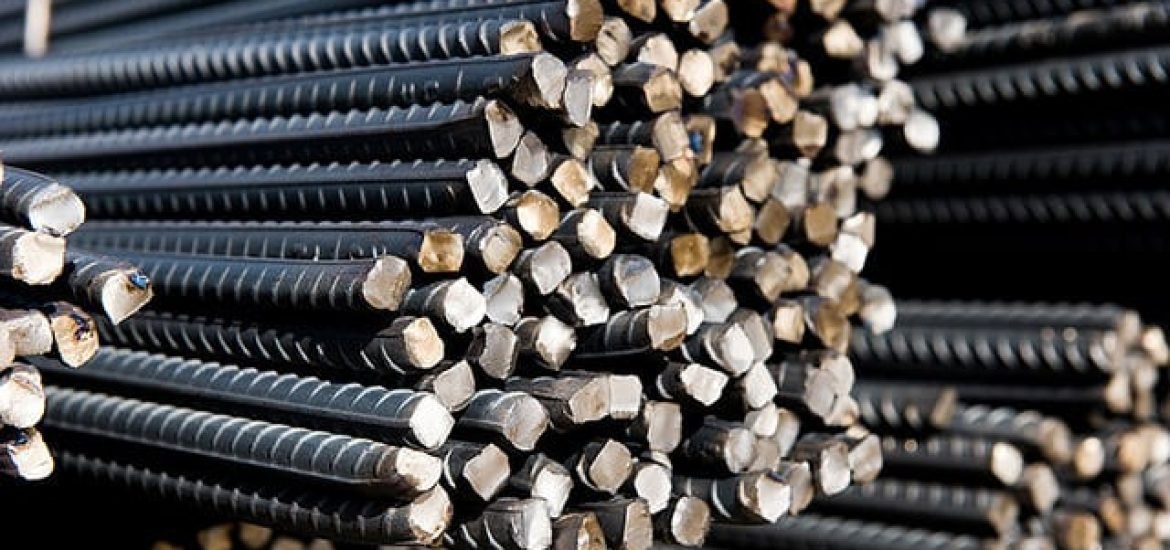
Stahl ist ein fester Bestandteil der weltweiten Industrie. Vor allem im Bau- und Transportwesen wird viel Stahl verbaut. Aber auch im Alltag findet man den Werkstoff überall, zum Beispiel in Messern und Pfannen. Insgesamt gibt es etwa 5.000 Stahlsorten auf dem Markt. Um die Qualitätsmerkmale der Sorten zu bestimmen, wurden bisher Proben von Experten visuell analysiert bewertet. Diese subjektive Methode der Klassifizierung ist stark von der Erfahrung des Betrachters abhängig und damit fehleranfällig. Materialforscher und Informatiker haben jetzt ein objektives Verfahren entwickelt, mit dem Computer die Werkstoff-Klassifizierung übernehmen können.
Produktive Zusammenarbeit zweier Disziplinen
An der Universität des Saarlandes ist es Wissenschaftlern aus zwei unterschiedlichen Disziplinen gelungen, ein objektives Verfahren zur Qualitätsanalyse von Stahlprodukten zu entwickeln. „Für uns ist das erst der Beginn einer intensiven Zusammenarbeit mit der hochkarätigen Informatikforschung auf dem Saarbrücker Uni-Campus. Wir gehen davon aus, dass sich unsere Ergebnisse auch auf viele andere Produktionsprozesse und Materialien übertragen lassen“, erläutert Uni-Professor für Materialforschung Frank Mücklich. Er und Mitarbeiter des von ihm geleiteten Steinbeis-Forschungszentrums für Werkstofftechnik arbeiteten für das Projekt eng mit Informatikern zusammen. Eine erfolgreiche Kooperation zwischen Forschungsdisziplinen ist nicht immer leicht. Häufig müssen alle zuerst einmal lernen, die gleiche Sprache zu sprechen. Das ging auch Dominik Britz, Doktorand, und seinen Kollegen so. „Bei uns hat es einige Zeit gedauert, bis die Informatiker verstanden haben, warum für uns Materialforscher die inneren Strukturen eines Materials und deren bildliche Darstellung eine so große Rolle spielen“. Die inneren Strukturen eines Materials sind nämlich eng mit seinen Eigenschaften verknüpft.
Bis jetzt brauchte es das geschulte Auge eines Experten
Für die Klassifizierung eines Werkstoffs wie Stahl werden Mikroskopie-Aufnahmen mit Beispielbildern verglichen. Verschiedene Stahltypen zeichnen sich durch jeweils typische geometrische Gefügestrukturen aus. Das zu erkennen braucht ein geschultes Auge. Deshalb werden in der Regel erfahrene Ingenieure zur Qualitätssicherung von Stahlprodukten eingesetzt. Britz wirft jedoch ein: „Auch ein geübter Experte kann sich täuschen, da die Bildabweichungen manchmal mit bloßem Auge kaum zu erkennen zu sind. Wir Menschen sind recht gut darin, kleine relative Unterschiede zu sehen, aber wir können nur schlecht absolute geometrische Standards wiedererkennen.“
Eine Vielzahl moderner Stahlvarianten lässt sich immer schwerer unterscheiden. Die Unterschiede finden sich in Mikrostrukturen, die selbst für einen geschulten Experten nur mit einer Genauigkeit von 50 Prozent bestimmt werden können.
Wie haben die Computer gelernt, Stahl zu klassifizieren?
Dazu ist es sinnvoll zu wissen, wie die Stahlproduktion abläuft. „Die Herstellung von Spezialstählen ist von vielen Faktoren abhängig. Die chemische Zusammensetzung, das verwendete Walzverfahren oder verschiedenen Wärmebehandlungen beeinflussen die geometrischen Gefügestrukturen. Jeder Produktionsschritt hat Auswirkungen auf die inneren Strukturen des Stahls“, erläutert Dominik Britz.
Um der Vielfalt und Komplexität gerecht zu werden, suchten die Materialforscher nach einem objektiven Verfahren, dass in der Lage ist, die Mikrostrukturen zu erkennen und auszuwerten. Ziel war auch die Entwicklung eines Programms, das ohne fachliche Kenntnisse des Anwenders sichere Ergebnisse liefert.
Um das möglich zu machen, wendeten die Informatiker ein Deep-Learning-Verfahren an, mit dem der Computer „lernen“ sollte, Stahlstrukturen zu erkennen. Hierfür wurden die Hochleistungsrechner mit Bilddaten gefüttert, durch zuvor durch das Auge eines Experten klassifiziert worden waren. Mithilfe dieser Bilder wurden die Computermodelle trainiert, Gefügestrukturen in Stahl zu erkennen, zu vergleichen und zu klassifizieren. Mit dem neuen Verfahren ist es jetzt erstmals möglich, die Mikrostrukturen von Stahl in einer Detailschärfe zu bestimmen, die bei subjektiven Methoden nicht möglich ist. „Unser System erreicht eine Klassifikationsgenauigkeit von rund 93 Prozent“, sagt der Materialforscher.