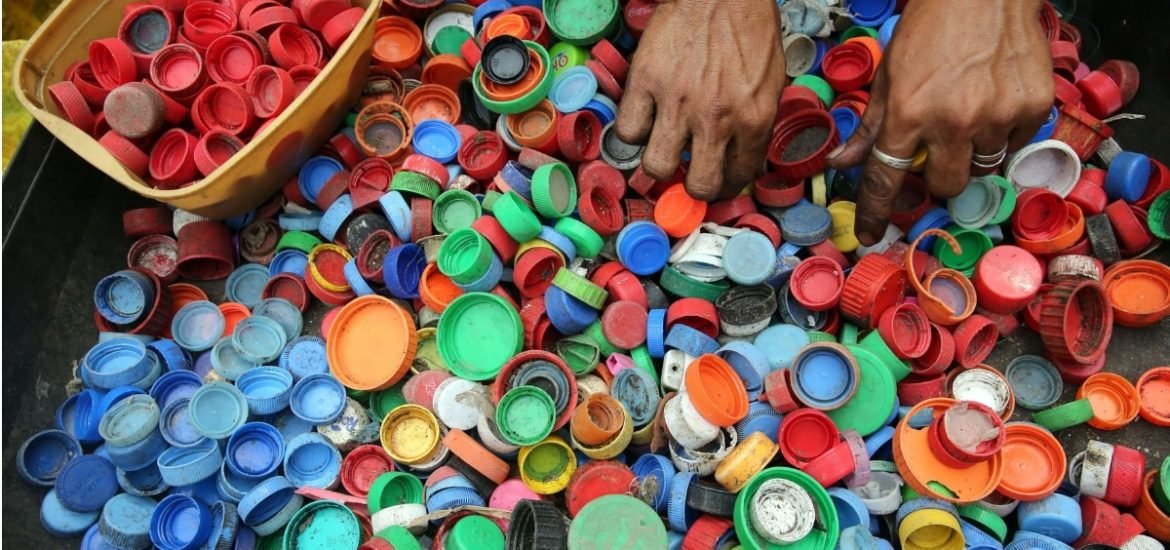
In a new study published in the January 2019 edition of Bioresource Technology, scientists have demonstrated an environmentally friendly method for the offshore production of bioplastics in large quantities (1). The process does not require the use of precious agricultural land or freshwater resources and could pave the way for the sustainable production of bioplastics in countries like Israel, China, and India, where water is scarce and plastic pollution is a major issue.
Global plastic consumption is currently at 320 million tonnes per annum and continues to increase, which will sadly lead to even more pollution of both lands and oceans. Moreover, the industrial process to produce plastics typically uses petroleum products, and chemical contaminants are released, further polluting the environment.
Biopolymers are emerging as potential alternatives to traditional plastics for many applications, such as packaging as well as disposable cutlery, pots, bowls, and straws. Bioplastics degrade quickly and could be used to replace some synthetic plastics. Furthermore, materials like starch, cellulose, wood, sugar, and biomass can be used as a substitute for fossil fuels during production, which could also make the process more sustainable. However, growing the plants and the bacteria required to make bioplastics still requires the use of fertile soil and fresh water, which are often scarce resources.
Polyhydroxyalkanoate (PHA) is a type of degradable plastic naturally produced by many microorganisms, for example, via bacterial fermentation of sugar or fats. The natural polyester is completely biodegradable, produce zero toxic waste, and can be fully recycled into organic waste. This type of bioplastic is already being produced in commercial quantities but still requires the use of plants that take up valuable agricultural land and fresh water.
Halophiles, such as Haloferax Mediterranei, are salt-loving organisms that have been shown to produce PHA in conditions similar to saltwater and therefore show promise for the offshore large-scale production of bioplastics (2). While the production process can be carried out in seawater and therefore, avoids the use of land and fresh water, it still requires a carbon source. Previous studies have looked at traditional biomass sources, including starch, byproducts of the ethanol industry, and cheese whey, but these do not provide a fully sustainable solution. Macroalgae, on the other hand, do not require land to grow and therefore do not compete with conventional food sources thereby offering a promising carbon source for the production of bioenergy and bioproducts (2).
The team of researchers from Tel Aviv University screened seven seaweed species as a potentially sustainable carbon source for PHA production by Haloferax Mediterranei. Their findings showed that seaweed could potentially be used as a fully sustainable and environmentally friendly carbon source for the production of PHA. Moreover, they found that green macroalgae from Ulva lactuca, or sea lettuce, has the greatest potential for PHA production.
Although biopolymers are only a partial solution to the growing plastic epidemic, this new process could make a significant contribution to reducing plastic in the world’s oceans without using up precious freshwater and land resources.
(1) Ghosh, S. et al. Macroalgal biomass subcritical hydrolysates for the production of polyhydroxyalkanoate (PHA) by Haloferax mediterranei. Bioresource Technology (2019). DOI: 10.1016/j.biortech.2018.09.108
(2) Yin, J. et al. Halophiles, coming stars for industrial biotechnology. Biotechnoly Advances (2015). DOI: 10.1016/j.biotechadv.2014.10.008
(3) Fernand, F. et al. Offshore macroalgae biomass for bioenergy production: Environmental aspects, technological achievements and challenges. Renewable Sustainable Energy Reviews (2017). DOI: 10.1016/j.rser.2016.10.046
Hopefully, there will also be researches on the effects of bioplastics to marine life. Finding alternatives to traditional plastics is good but we also need to find a solution to the existing pollution.